When it comes to contract manufacturing, one common aspect that businesses encounter is Minimum Order Quantities (MOQs). These requirements can play a significant role in determining the feasibility and affordability of outsourcing your product manufacturing. In this blog post, we'll delve into the world of MOQs, explaining what they are, how they work, and why they are important considerations in contract manufacturing.
Understanding Minimum Order Quantities (MOQs):
Minimum Order Quantity refers to the minimum number of units or products that we require our clients to order per production run. This requirement ensures that the manufacturing process remains economically viable for both parties involved. MOQs can vary widely, depending on factors such as:
- Product complexity
- Production capabilities
- Raw materials
- Batch size
- Fragrance
- Packaging components
Factors Influencing MOQs in Contract Manufacturing:
- Production Efficiency: We aim to optimize our production processes to maximize efficiency. MOQs are often set to ensure that production lines can run smoothly and cost-effectively. Higher MOQs can help us achieve economies of scale, reducing unit costs and making the production process more efficient.
- Raw Material Procurement: MOQs can also be influenced by the minimum quantities required for sourcing raw materials. Suppliers of raw materials may have their own MOQs, and we need to ensure that we can meet these requirements while maintaining consistency in our supply chain.
- Set-up Costs: Setting up the production line for a specific product incurs certain costs, such as equipment setup, tooling, labor, and preparation. MOQs help us recover these costs by ensuring that a sufficient volume of products is produced within each run.
Benefits and Considerations of MOQs:
- Cost Efficiency: MOQs often enable us to optimize our production and achieve lower unit costs. By ordering larger quantities, we can benefit from economies of scale and potentially secure more competitive pricing.
- Inventory Management: While MOQs may require larger order quantities, they can help businesses maintain an appropriate level of inventory. By ordering in bulk, companies can better manage their stock and ensure consistent product availability.
- Financial Considerations: It is essential to carefully evaluate the financial implications of MOQs. Higher MOQs may require larger upfront investments, which need to be balanced with demand forecasts, budget constraints, and market considerations. Please note that ordering the lowest MOQ available likely will not be the most cost effective route.
Minimum Order Quantities (MOQs) form an integral part of our business, impacting various aspects of the production process and cost structure. Understanding MOQs and their underlying factors is crucial for businesses seeking to outsource their manufacturing operations. By grasping the significance of MOQs and evaluating their implications in the context of your specific requirements, you can make informed decisions, ensuring a successful and mutually beneficial partnership.
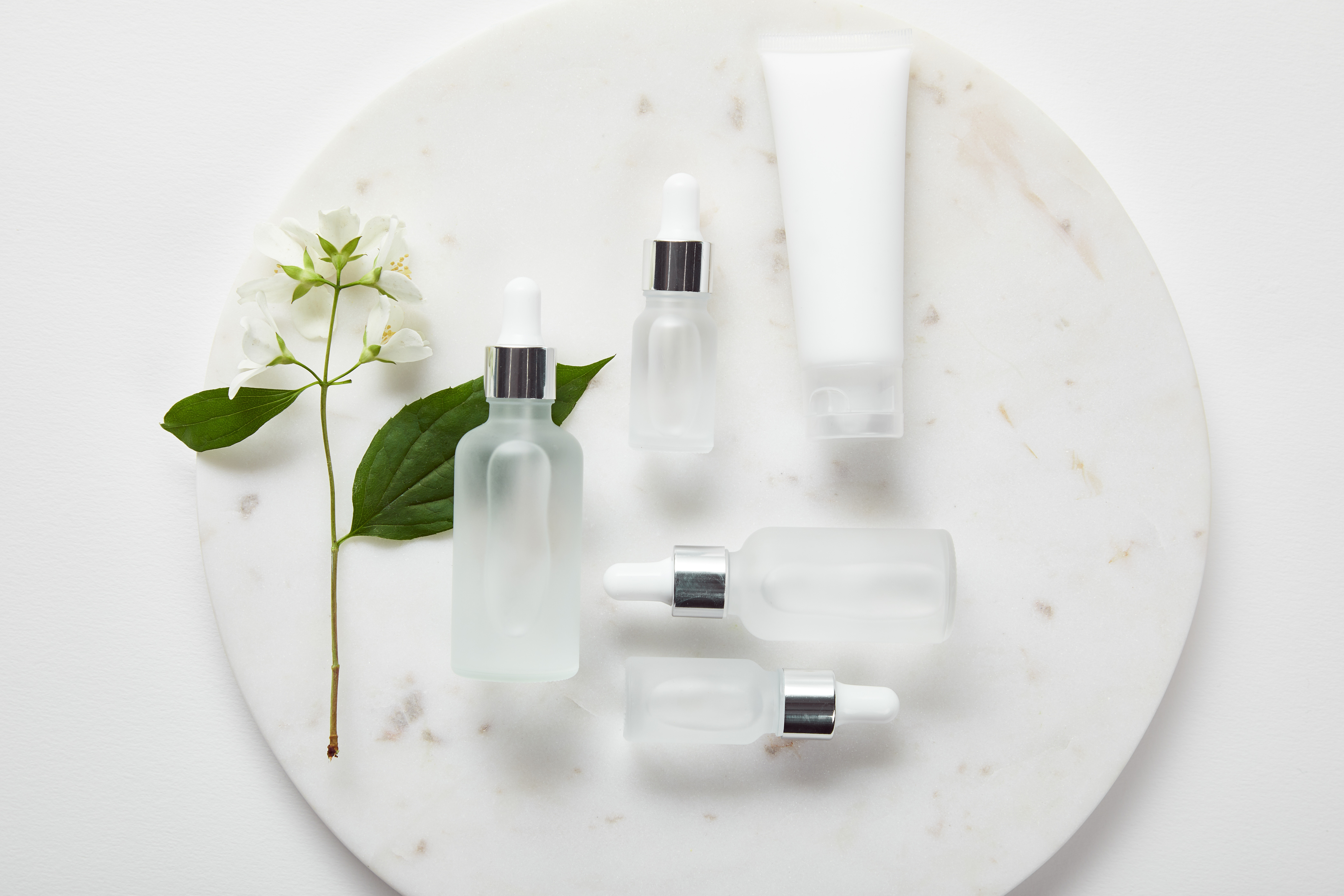